Epoxy fr4 sheet vs carbon fiber plate
2024-07-03 11:16 | By: ZTELEC-www.ztelecgroup.com | 131click
Difference between FR4 and Carbon Fiber
Definition of FR4 and Carbon Fiber
FR4: FR-4 (or FR4) is a NEMA grade designation for glass-reinforced epoxy laminate material. It is a composite material composed of woven fiberglass cloth with an epoxy resin binder that is flame resistant (self-extinguishing).
Carbon Fiber: Carbon fibers (alternatively CF, graphite fiber or graphite fibre) are fibers about 5 to 10 micrometers in diameter and composed mostly of carbon atoms.
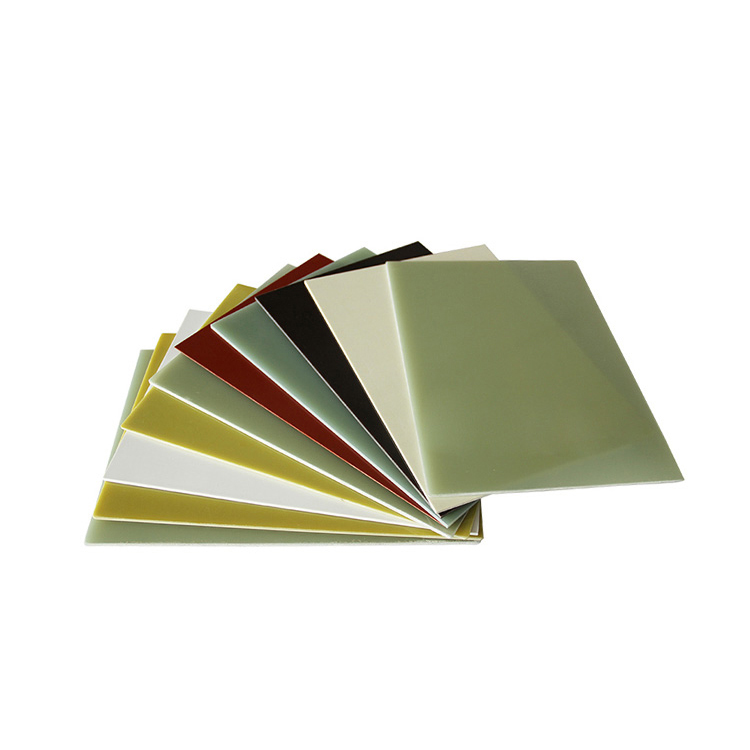
FR4 vs. Carbon Fiber Manufacturing
FR4: The manufacturing process of FR4 involves several carefully controlled steps1234. Here’s a brief overview:
Material Design: The material design of FR4 involves a meticulous arrangement of glass cloth layers impregnated with high-quality epoxy resin.
Preparation: Certain fillers improve properties like the comparative tracking index, the dielectric strength, and fire retardancy.
Lamination: The fiberglass sheets are impregnated with epoxy resin and covered with a copper foil layer. This entire construction is then placed in a press, which bonds it into a single FR4 sheet.
Fabrication: FR4 material is available in different forms to suit diverse manufacturing needs or applications.
Carbon Fiber: The carbon fiber production process is an intricate dance of chemistry and engineering. Here’s a brief overview:
Spinning: Polyacrylonitrile (PAN) is mixed with other ingredients and spun into fibers, which are washed and stretched.
Stabilization: The PAN fibers are heated in the presence of oxygen, which stabilizes their molecular structure and prepares them for the intense heat they’ll face in the carbonization stage.
Carbonization: The stabilized fibers are exposed to very high temperatures in an oxygen-free environment. This process ensures that all non-carbon atoms are expelled from the PAN fibers, leaving behind a fiber composed almost entirely of carbon atoms.
Surface Treatment and Sizing: The carbon fibers’ bond compatibility with various resins improves by slightly oxidizing the fiber’s surface or etching it with certain chemicals.
FR4 and Carbon Fiber Mechanical Properties: Strength vs. Rigidity
the mechanical properties of strength and rigidity.
Strength: Strength is a measure of the maximum stress that a material can withstand without failure. It’s the ability of a material to resist deformation under load.
Rigidity: Rigidity, on the other hand, is a measure of a material’s resistance to deformation under an applied force. It’s often associated with the stiffness of a material.
the context of FR4 and Carbon Fiber:
FR4: FR4 is known for its high mechanical strength, making it suitable for applications requiring robust structural support. It exhibits good rigidity and impact resistance, making it a preferred material in industries such as electronics and construction. FR4’s fiberglass reinforcement provides the material with excellent mechanical strength, while the epoxy resin adds structural rigidity and dimensional stability.
Carbon Fiber: Carbon fiber boasts an extraordinary strength-to-weight ratio, providing exceptional tensile strength and stiffness. Its lightweight nature and superior mechanical properties make carbon fiber ideal for high-performance applications in aerospace and automotive industries. Carbon fiber also happens to boast a high rigidity in addition to high strength.
FR4 and Carbon Fiber Weight dfferident
FR4: While robust, FR4 has a higher density compared to carbon fiber, making it a slightly heavier material. The density of FR4 typically ranges from 1.7 to 1.9 grams per cubic centimeter (g/cm³)1. This characteristic may influence material selection in applications where weight is a critical factor.
Carbon Fiber: Carbon fiber’s lightweight nature contributes to its widespread use in applications where minimizing mass is crucial. In terms of weight, carbon fiber plates are significantly lighter than their FR4 counterparts – often between 30-60% lighter. It is a preferred choice in industries seeking materials that provide strength without adding significant weight.
In summary, both FR4 and Carbon Fiber have good strength-to-weight ratios, but Carbon Fiber is significantly lighter, making it more suitable for applications where weight is a key factor.
FR4 and Carbon Fiber Electrical Insulation vs. Conductivity: Contrasting Roles
the contrasting roles of electrical insulation and conductivity
Electrical Insulation: Electrical insulation refers to a material’s ability to resist the flow of electric current. Insulators are materials that do not allow electric charges to flow freely. The atoms of an insulator have tightly bound electrons which cannot readily move.
Electrical Conductivity: Electrical conductivity, on the other hand, refers to a material’s ability to conduct electric current. Conductors are materials that allow the flow of electric charges.
in the context of FR4 and Carbon Fiber:
FR4: FR4 is an effective electrical insulator. It prevents electrical current from flowing between the conductive traces on a PCB. However, FR4 does not offer good thermal conduction, with a conductivity level below 1W/mK (watts per Kelvin). This makes it a poor conductor with low ability to dissipate heat. But, the presence of copper in a PCB made of this material improves the conductivity by a small margin.
Carbon Fiber: Carbon fiber, conversely, has conductive properties, and it is sometimes used as a reinforcement in applications requiring electrical conductivity. It is not an ideal electrical insulator because it has extremely strong conductivity. Carbon fiber majorly contains carbon (about 95%) and metal electron gas on both sides which give a conductivity similar to or more than that of metals.
Applications: Tailoring Materials to Specific Needs
materials like FR4 and Carbon Fiber can be tailored to meet specific needs in various applications.
FR4: FR4 is a widely used material in the manufacturing of printed circuit boards (PCBs). Its versatility, durability, and excellent electrical properties make it indispensable in modern electronics. FR4 is also used in electrical insulators and automotive components. Its reliability, stability, and flame-retardant properties make it a go-to choice for critical applications. It’s used in various industries, including consumer electronics, industrial controls, power electronics, high-frequency applications, automotive electronics, and aerospace and defense applications.
Carbon Fiber: Carbon fiber has found wide applications in commercial and civilian aircraft, recreational, industrial, and transportation markets. It’s used in composites with a lightweight matrix, making it ideally suited to applications in which strength, stiffness, low weight, and outstanding fatigue characteristics are critical requirements. Carbon fiber is also used in sports equipment, military protective equipment, weapons, drones, knives, workboots, hardhats, watches, canoes, musical instruments, and building supplies such as trusses and structural beams. It’s also used in wind turbines, automotive, marine, and infrastructure.
FR4 and Carbon Fiber pice
the price considerations of FR4 and Carbon Fiber:
FR4: The price of FR4 PCB material can vary based on factors such as thickness, copper cladding, surface finish, and quantity ordered. Generally, the price ranges from a few dollars per square foot for standard FR4 material to higher costs for specialized variants or custom specifications. Some sources suggest that the price for FR4 ranges from $0.43 to $0.67 per piece, and others suggest a price range of $2.80 to $3.30.
Carbon Fiber: The price of carbon fiber is generally higher than traditional materials such as steel or aluminum. However, when considering the strength-to-weight ratio, carbon fiber is often the more economical option. For instance, industrial-grade carbon fiber used to cost as much as $15 per pound; now it can cost as little as $7 per pound. In Q3 2023, carbon fiber prices reached 1184 USD/MT in the USA, 1358 USD/MT in South Korea, and 1185 USD/MT in Germany.
In summary, both FR4 and Carbon Fiber have different price points due to their unique properties and manufacturing processes.
Choosing Between FR4 and Carbon Fiber
Choosing between FR4 and Carbon Fiber depends on the specific requirements of your application. Here are some factors to consider:
Strength and Rigidity: Carbon fiber has a higher strength-to-weight ratio and is stiffer than FR4. If your application requires high strength and rigidity, carbon fiber might be the better choice.
Electrical Properties: FR4 is an excellent electrical insulator, making it suitable for applications like printed circuit boards. On the other hand, carbon fiber has conductive properties. If your application requires electrical insulation, FR4 would be the better choice. If it requires conductivity, then carbon fiber would be more suitable.
Weight: Carbon fiber is significantly lighter than FR4. If weight is a critical factor in your application, carbon fiber might be the better choice.
Cost: Carbon fiber is generally more expensive than FR4. If cost is a significant factor, FR4 might be the more economical choice.
Thermal Properties: FR4 has poor thermal conduction, while carbon fiber has good thermal properties. If your application requires good thermal conductivity, carbon fiber might be the better choice.
tags:transformer voltage conversionelectromagnetic inductionstep-up transformertransformer advantagesdry-type transformer
- more+releated article
- 2025-06-05How Does a Transformer Transform Voltage? In-D
- 2025-06-05How to Choose DDP Diamond Pattern Paper for Yo
- 2025-06-04Dry-Type Transformers: Technical Conditions, A
- 2025-06-04Live from the CWIEME Berlin | Highlights from
- 2025-06-03Advantages of Dry-Type Transformers: Performan
- 2025-05-30Custom-Cut G11 Fiber Sheets: How to Order the
- 2025-05-30Transformer Voltage Conversion: Principle and
- 2025-05-29Causes and Solutions of Dry-Type Transformer E
- 2025-05-29How G11 Fiber Sheets Improve High-Temperature
- 2025-05-28Technical Parameters and Performance Features