what is bakelite products and how to make bakelite?
2024-08-22 14:20 | By: ZTELEC-www.ztelecgroup.com | 95click
what is bakelite
Bakelite is a synthetic plastic that was invented by chemist Leo Baekeland in 1907. Formally known as polyoxybenzylmethyleneglycolanhydride, Bakelite is a thermosetting phenol-formaldehyde resin created through a condensation reaction between phenol and formaldehyde. This process results in a hard, infusible, and chemically resistant material that cannot be reshaped once cured.
Historical Significance
Bakelite is recognized as the first fully synthetic plastic, marking a significant advancement in materials science. Its invention paved the way for the modern plastics industry, as it was the first synthetic resin to be commercially produced. Baekeland's work not only led to the establishment of the General Bakelite Company in 1910 but also inspired the development of other synthetic plastics, transforming the chemical industry at the time, which primarily focused on dyes and explosives.
Properties and Applications
Bakelite is known for its excellent electrical insulation, heat resistance, and durability, making it suitable for a wide range of applications, including:
Electrical Components: Used in insulators, switchboards, and casings for radios and telephones.
Automotive Parts: Found in ignition systems, distributor caps, and other non-conductive components.
Household Items: Commonly used in kitchenware, jewelry, and various consumer goods.
Industrial Uses: Employed in manufacturing durable parts and components due to its mechanical strength and resistance to chemicals.
Today, Bakelite is still used in specific applications requiring its unique properties, although many decorative uses have diminished, making vintage Bakelite items collectible.
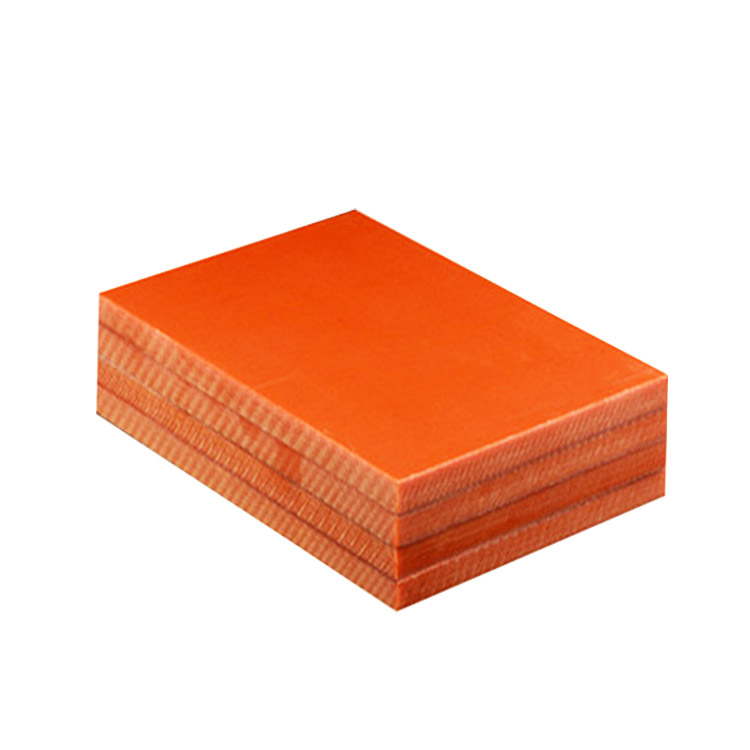
Bakelite Products What are they?
Bakelite was a revolutionary synthetic plastic invented in 1907 by Leo Baekeland. It was the first fully synthetic plastic material and found widespread use in a variety of products due to its unique properties. Some of the most common Bakelite products include:
Electrical Components
Switchboards, panels and sockets for light bulbs
Bases and sockets for radios and electron tubes
Supports for electrical components
Automobile distributor caps and other insulators
Automotive Parts
Ignition apparatus
Radiator caps
Steering wheels
Household Items
Knobs and dials for radios
Handles for irons and other appliances
Dominoes, mah-jongg tiles, checkers, and chess pieces
Jewelry and Novelties
Costume jewelry
Various novelty items
Other Applications
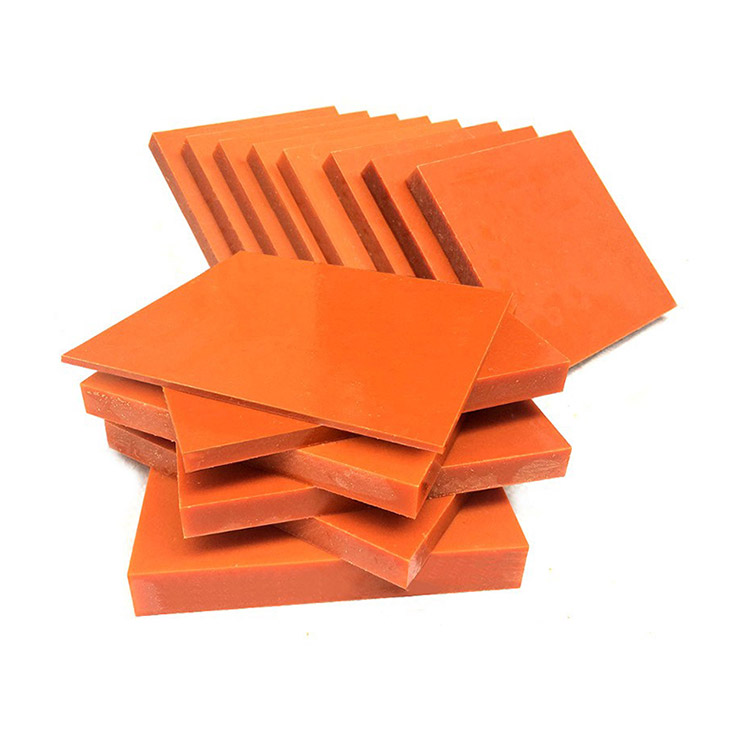
how to make bakelite
Making Bakelite involves a multi-step process primarily centered around the reaction between phenol and formaldehyde. Here’s a detailed overview of how Bakelite is synthesized:
1. Synthesis of Bakelite Resin
The first step in making Bakelite is the synthesis of the phenol-formaldehyde resin:
Reagents: The primary materials are phenol and formaldehyde. A catalyst, such as hydrochloric acid or zinc chloride, is often used to facilitate the reaction.
Condensation Reaction: Phenol and formaldehyde are heated together, resulting in a liquid condensation product known as Bakelite A. This initial product is soluble in alcohol and acetone.
Further Heating: As the mixture is heated further, it transitions to a more complex structure. Continued heating leads to the formation of an insoluble hard gum, which is the basis for Bakelite. This process must be carefully controlled to avoid excessive foaming and ensure the final product is dense and hard.
2. Molding Process
Once the Bakelite resin is prepared, it can be molded into various shapes:
Compression Molding: The resin can be combined with fillers (like wood flour) and placed in a mold. The mold is then subjected to high pressure and heat, typically around 150 °C (302 °F). This curing process solidifies the resin into a hard plastic material.
Layering for Sheets: For Bakelite sheets, layers of paper or fabric can be impregnated with Bakelite resin. These layers are stacked and pressed together in a hydraulic press to form solid sheets. The sheets can then be cut or machined into desired shapes using CNC machining.
3. Final Properties
The resulting Bakelite is a thermosetting plastic, meaning it cannot be remolded after curing. It is characterized by:
High Mechanical Strength: Bakelite is durable and resistant to wear.
Electrical Insulation: It is an excellent insulator, making it suitable for electrical applications.
Heat Resistance: Bakelite can withstand high temperatures without deforming.
This process allows Bakelite to be used in various applications, from electrical components to household items and automotive parts
tags:150KVA transformertransformer for medical equipmentthree-phase isolation transformerdry-type transformerenergy efficient transformer
- more+releated article
- 2025-06-16High-Performance GPO-3 Sheets for Electrical I
- 2025-06-16Top 5 Advantages of 150KVA Three-Phase Isolati
- 2025-06-13Treatment Methods for Cracks in the Steel Core
- 2025-06-13[Ztelecgroup Mid-Year Promotion] Special Offer
- 2025-06-12Advantages and Disadvantages of GPO-3 Sheets i
- 2025-06-12Top Noise Sources in Isolation Transformers an
- 2025-06-11GPO-3 Laminate Sheet: Benefits, Limitations &a
- 2025-06-11The Future of Power Distribution: Why Dry-Type
- 2025-06-10hy Are 35kV Transformers More Compact Than 10k
- 2025-06-09Innovations and Breakthroughs in Dry-Type Tran