product description
1.G-10 sheet introduction
G-10 is a fiberglass-reinforced epoxy composite material consisting of woven glass fibers and an epoxy resin adhesive. That is, made of woven fiberglass cloth impregnated with epoxy resin. There may be some variation in its performance parameters because different manufacturers and products may have different formulations and manufacturing processes.
As a glass fiber reinforced epoxy resin composite, G-10 has several advantages that make it widely used in a variety of applications. It has excellent insulation properties, mechanical strength and chemical corrosion resistance.
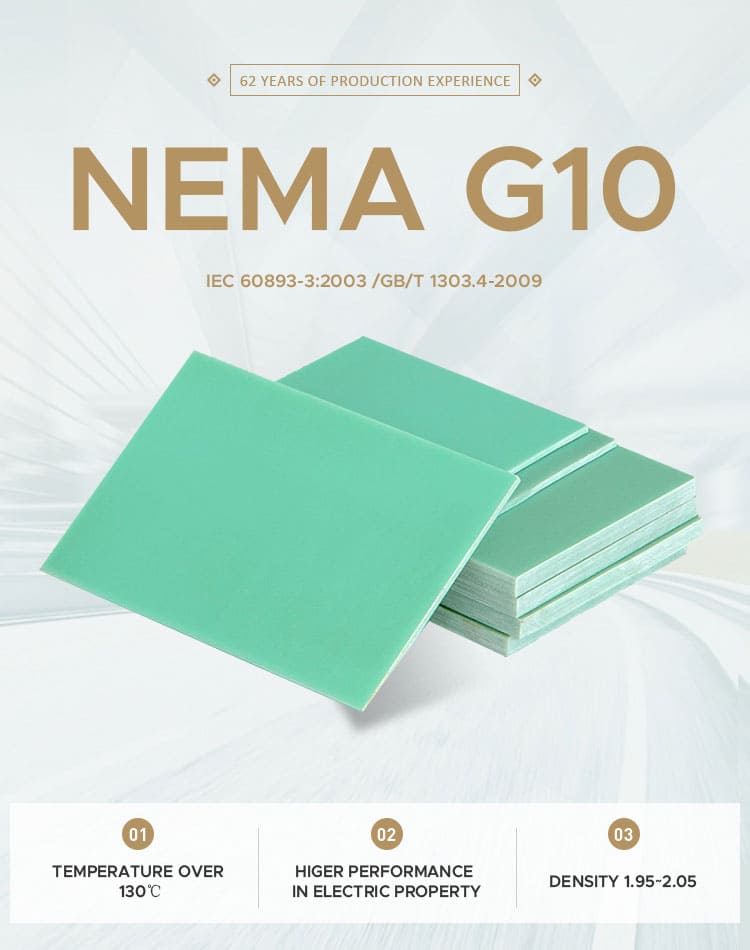
2. How is G-10 made?
G-10 is a glass fiber reinforced epoxy resin composite material. Its manufacturing process mainly includes the following steps:
Material preparation:
Epoxy resin: Choose an appropriate epoxy resin as the base material, usually bisphenol A or bisphenol F epoxy resin.
Fiberglass Cloth: Choose fiberglass cloth or elongated fiberglass prepreg, which is a reinforcement material that provides strength and stiffness.
Stacking:
Layer by layer of fiberglass cloth pre-impregnated with epoxy resin. During this process, depending on the design and requirements, the orientation of the fiberglass cloth can be changed to adjust the properties of the final composite.
Typically a layer of epoxy is applied between each layer to ensure complete infiltration of the fiberglass and create an even layer structure.
Heat curing:
The laminated material is placed in a mold and then thermally cured. During this stage, the epoxy polymerizes to form a strong matrix.
Temperature and time control are critical to ensure that the resin is fully cured to achieve designed performance.
Cutting and processing:
Once heat curing is complete, the G-10 composite is removed from the mold, cut and machined. This can be achieved through mechanical processing (such as cutting, drilling, grinding) to meet the shape and size requirements of the final product.
Surface treatment:
Depending on the requirements of the final product, surface treatment may be required. This includes polishing, coating or other surface treatment processes to improve appearance quality and performance.
The entire manufacturing process requires strict control of material ratios, prepreg impregnation uniformity, temperature and time of the thermal curing process to ensure consistent performance and quality of the final G-10 product. This composite material is widely used in electronics, machinery, aerospace and other fields due to its high strength, excellent insulation properties and corrosion resistance.
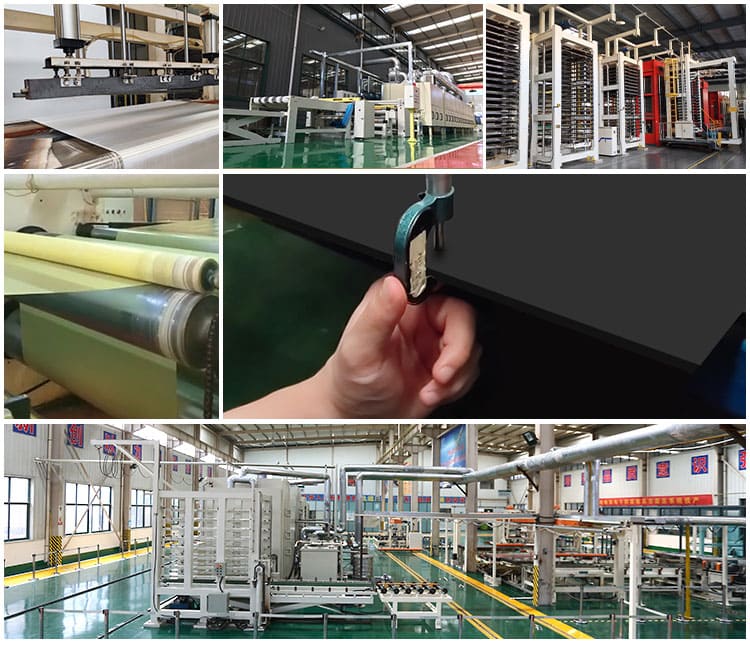
3.g10 data parameters
Some common typical data parameters of G-10, these values are for reference only:
Density: about 1.70-1.90 g/cm³.
Bending strength: Typical value is between 300-500 MPa.
Tensile strength: approximately between 200-400 MPa.
Flexural modulus (stiffness): approximately 20-40 GPa.
Tensile modulus: Approximately between 10-25 GPa.
Thermal expansion coefficient: Typical value is 12-17 μm/m·K.
Dielectric constant: Approximately between 4-5.
Dielectric strength: Typically between 50-150 kV/mm.
Glass transition temperature (Tg): Typical value is approximately 120-150°C.
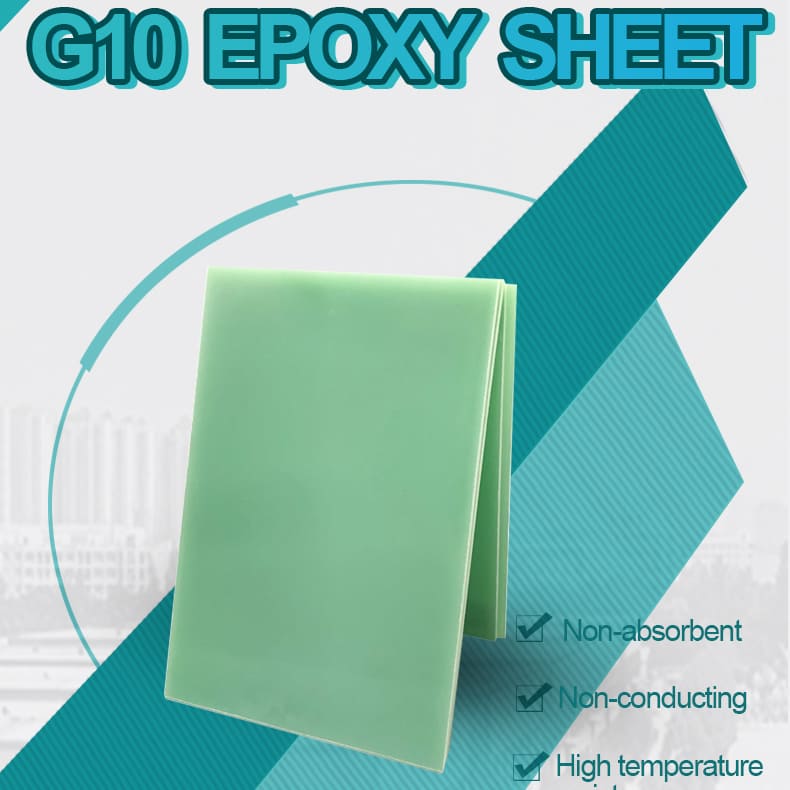
Please note that these values are for general reference only and actual products may vary. When selecting G-10 materials, appropriate product specifications should be selected based on the requirements of the specific application and refer to the technical data sheet provided by the manufacturer. Data sheets provided by manufacturers often contain more detailed and accurate material property information.
g10 data table
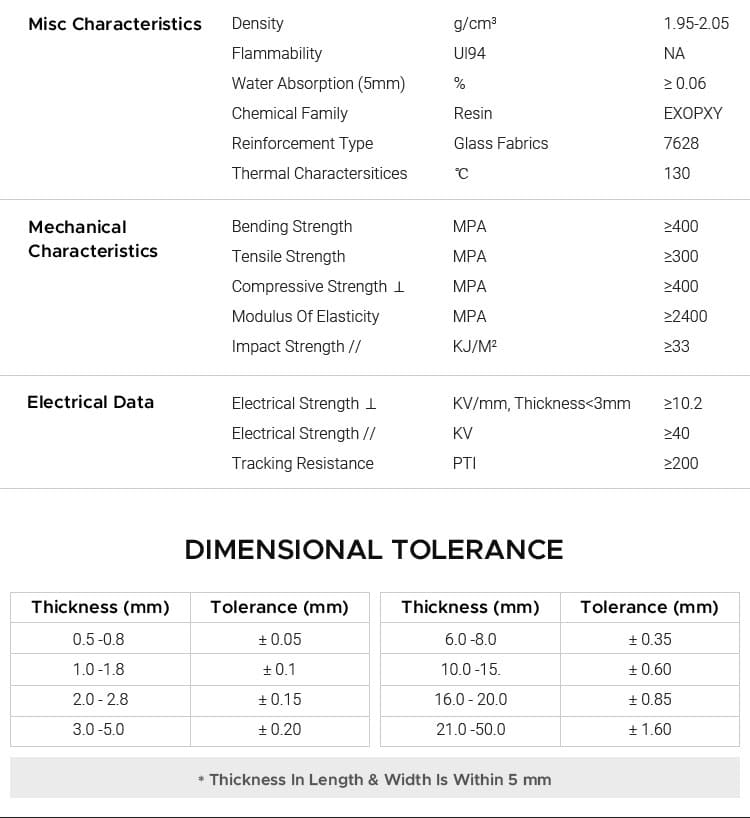
4.Benefits and advantages of g10
Here are some of the key benefits of G-10:
High Strength: G-10 has excellent strength, especially in the tensile and bending directions. This makes it ideal for manufacturing parts and structures that require high strength and stiffness.
Excellent insulation properties: G-10 has good insulation properties, making it an ideal material for manufacturing insulating components in electronic and electrical equipment. It is very good at isolating current and electric fields.
Corrosion resistance: G-10 has strong resistance to chemical corrosion, making it suitable for some environments that require high corrosion resistance.
Lightweight: G-10 is a relatively lightweight material, which helps reduce the weight of components and structures, which is very beneficial for applications that require lightweighting.
Good machining performance: G-10 material is easy to process and can be used for cutting, drilling, grinding and other processing operations to meet the requirements of various shapes and sizes.
Stability: G-10 maintains high dimensional stability over a wide temperature range and is not easily affected by temperature changes.
Wear Resistance: Due to its combination of fiberglass reinforcement and epoxy resin, G-10 exhibits good wear resistance and is suitable for some applications requiring wear resistance.
Flame retardancy: G-10 usually shows good flame retardancy at high temperatures, making it applicable in some situations that require high flame resistance.
Versatility: G-10 can be formulated according to specific application needs to obtain different performance characteristics, increasing its applicability in different fields.
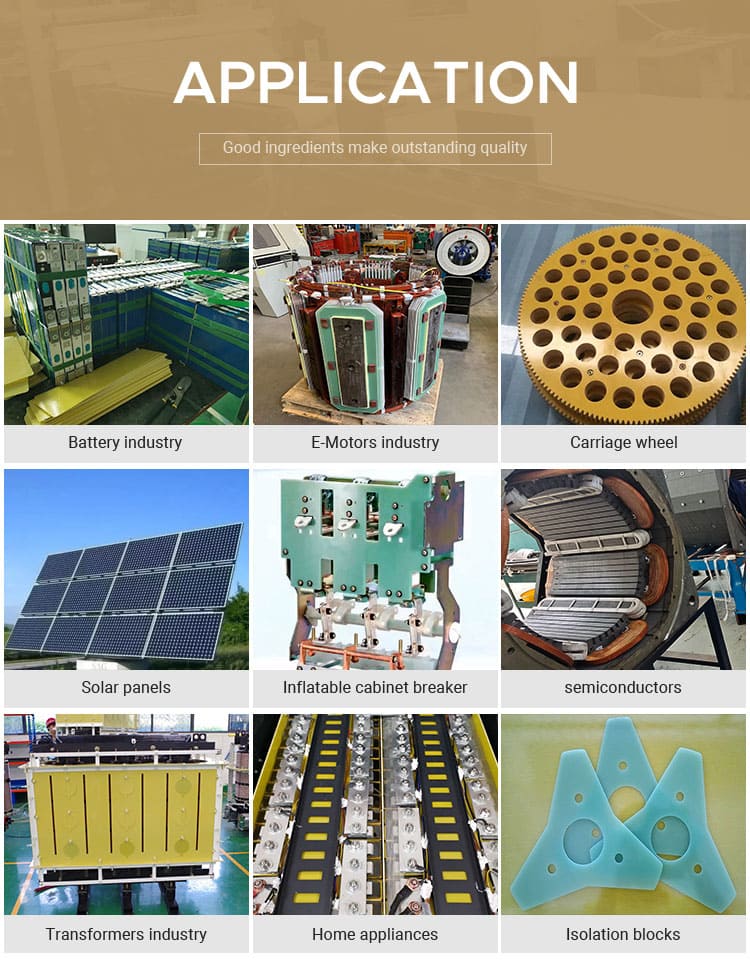
5.Application fields of G-10
Here are some of the main application areas of G-10:
Electronics and Electrical Engineering: G-10 is commonly used in the manufacture of insulating components for electronic and electrical equipment, such as insulating panels, partitions, insulating sleeves, etc. Its excellent insulation properties make it an ideal material for circuit boards (PCBs) and other electronic components.
Mechanical Engineering: Due to its high strength, rigidity and wear resistance, G-10 is suitable for manufacturing mechanical parts such as gears, bearing sleeves, spacers, etc. It can also be used to create a variety of structural and support components.
Aerospace: G-10's light weight and high strength make it useful in aerospace applications. It is often used in the manufacture of spacecraft parts, casings and structural parts of avionics equipment.
Medical devices: The chemical corrosion resistance and biocompatibility of G-10 make it have certain applications in the field of medical devices, such as the manufacture of shells and components of some medical devices.
Chemical Industry: G-10 is resistant to corrosion by many chemicals and is therefore used in some chemical industry applications to manufacture corrosion-resistant parts and equipment.
Shipbuilding industry: G-10's waterproof performance and salt spray resistance make it used in the shipbuilding industry to manufacture some structures and parts of ship equipment.
Sports and Recreation Equipment: The strength and abrasion resistance of G-10 give it potential applications in the manufacture of sports equipment and recreation equipment, such as premium sports equipment and outdoor gear.
Military field: G-10's high strength, corrosion resistance and electrical insulation properties enable it to be used in military equipment, such as manufacturing radar antennas and other military electronic equipment.
Overall, G-10 is widely used in many industries due to its multiple excellent properties. The range of uses for this material depends on how its properties meet the requirements of a specific application.
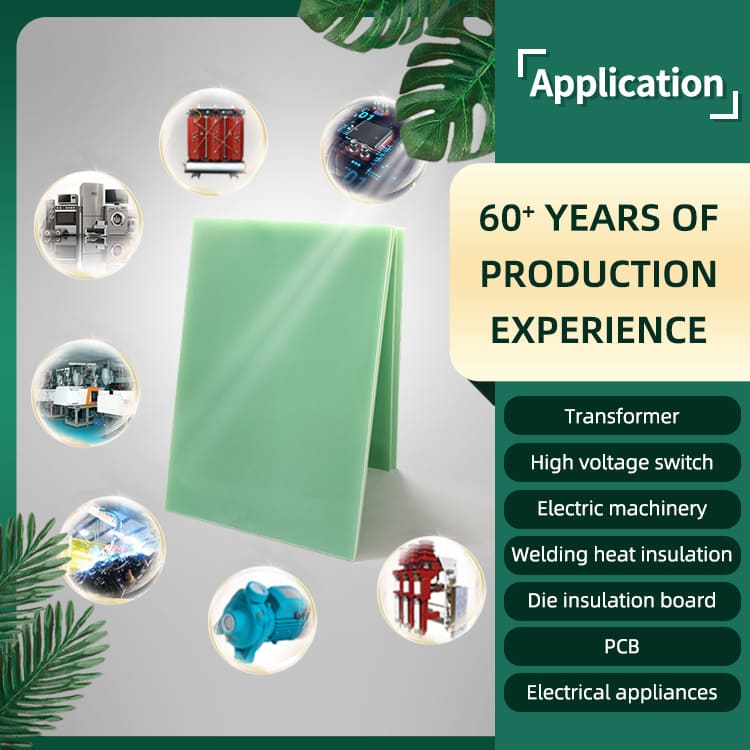
6.G-10 insulation material manufacturing plant
In China, the world's factory, there is an excellent epoxy insulation material manufacturer, namely ztelecgroup. They have their own company and factory, and they provide components for China's aerospace components, so the quality is very reliable. Therefore, finding such a factory will be more conducive to the long-term development of the company.
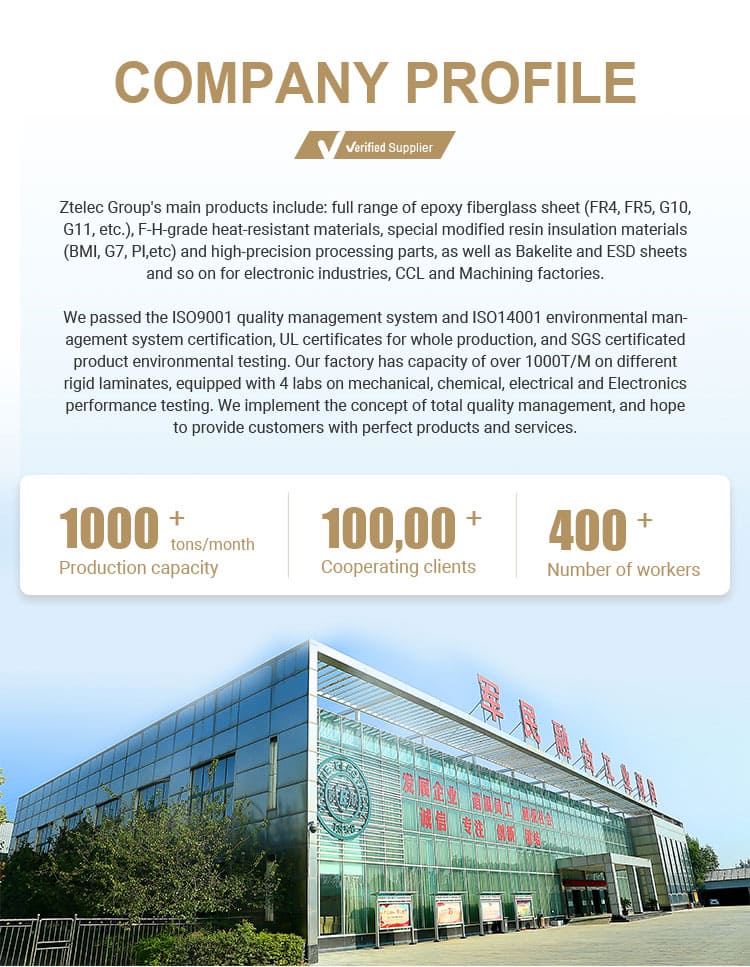
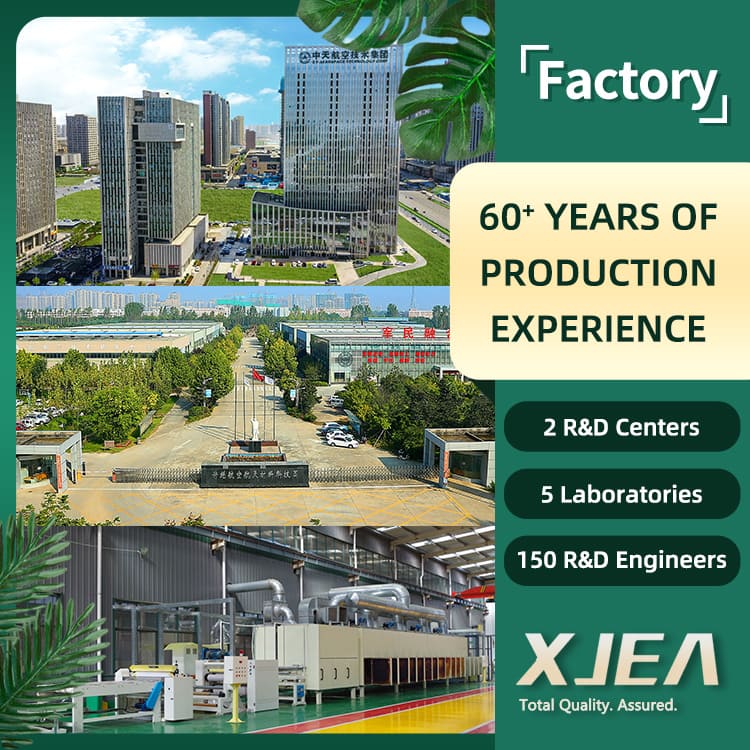