G-10 vs. FR4: A Comprehensive Comparison
2024-08-16 16:35 | By: ZTELEC-www.ztelecgroup.com | 61click
When it comes to choosing materials for printed circuit boards (PCBs) and various other industrial applications, G-10 and FR4 are two of the most commonly discussed options. Both are glass-reinforced epoxy laminates, known for their mechanical strength, electrical insulation properties, and moisture resistance. However, understanding the differences between G-10 and FR4 is crucial in selecting the right material for your specific needs.
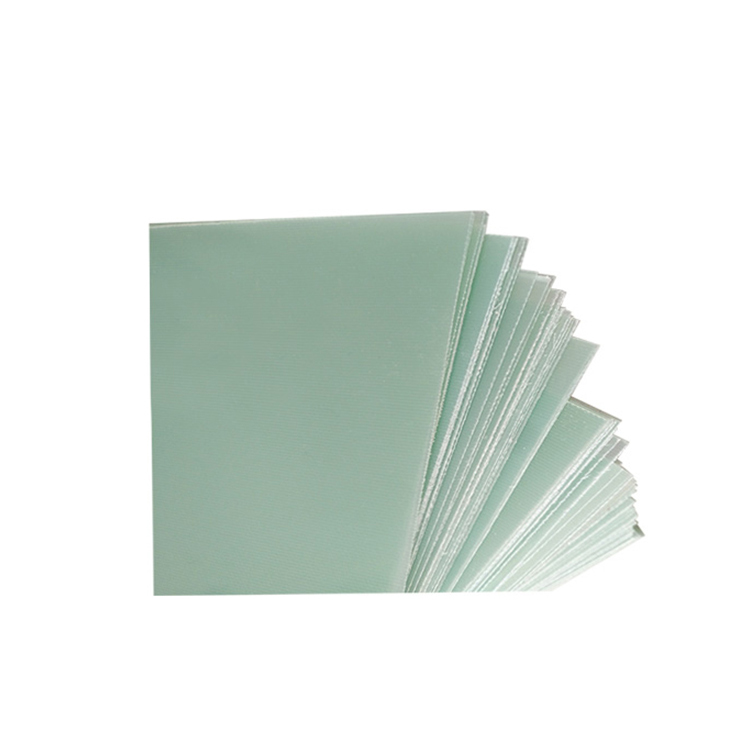
What is G-10?
G-10 is a high-pressure fiberglass laminate, a type of composite material. It is created by stacking multiple layers of woven glass cloth, which are then bonded together with epoxy resin under high temperature and pressure. G-10 is known for its high mechanical strength, low moisture absorption, and excellent dielectric properties.
Applications: G-10 is widely used in the electronics industry for PCB substrates, in the knife-making industry for handles, and in various other applications requiring strong, lightweight, and non-conductive materials.
Properties: High tensile strength, good dimensional stability, and resistance to chemical and environmental factors.
What is FR4?
FR4 is also a glass-reinforced epoxy laminate but with an additional property that sets it apart: flame retardance. The "FR" in FR4 stands for "flame retardant," indicating its ability to withstand fire, which is a crucial feature in many electronic applications.
Applications: FR4 is the most commonly used material in PCBs. Its flame retardant properties make it suitable for environments where fire safety is a concern.
Properties: Good electrical insulation, flame retardance, moisture resistance, and mechanical strength similar to G-10.
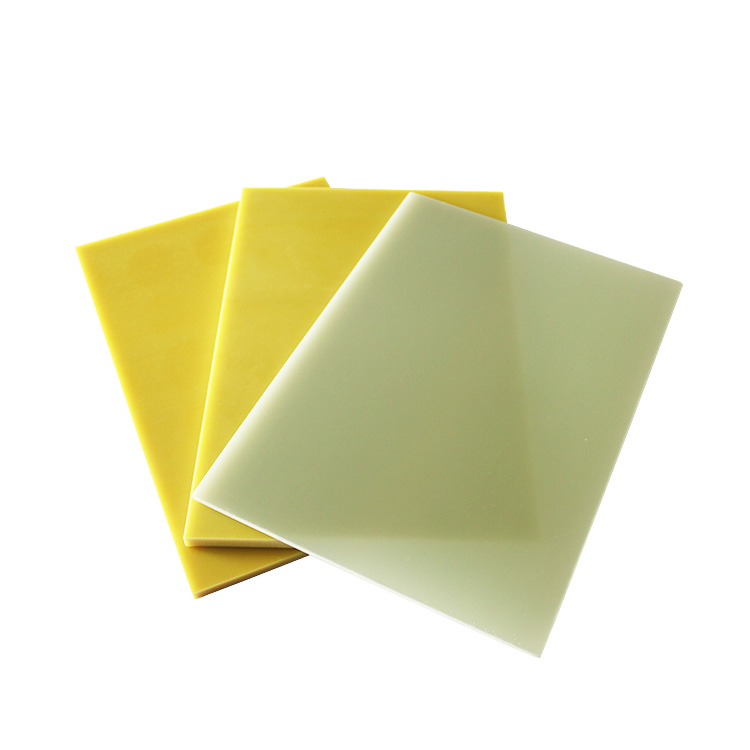
Key Differences Between G-10 and FR4
Flame Retardance:
G-10: Does not have flame retardant properties, which limits its use in certain environments where fire resistance is critical.
FR4: Contains a brominated compound that makes it flame retardant, making it the preferred choice for applications where fire safety is essential.
Cost:
G-10: Typically more expensive than FR4 due to its specific properties and applications.
FR4: Generally less expensive, largely because it is produced in higher volumes due to its widespread use in the electronics industry.
Applications:
G-10: Preferred in non-flammable environments or where fire retardance is not a primary concern. Common in knife handles, circuit board insulation, and other high-stress environments.
FR4: Dominates the PCB market and is used where flame resistance is a mandatory requirement, such as in consumer electronics, industrial control systems, and automotive electronics.
Mechanical Strength:
G-10: Marginally higher mechanical strength compared to FR4, making it suitable for applications that require extra durability.
FR4: While slightly less strong than G-10, it is still robust enough for most PCB applications and other industrial uses.
Dielectric Properties:
G-10: Offers excellent dielectric strength, making it suitable for high-voltage applications.
FR4: Also provides good dielectric strength, though slightly lower than G-10, it is adequate for most electronic applications.
Choosing Between G-10 and FR4
When selecting between G-10 and FR4, consider the specific requirements of your application:
If flame retardance is crucial, FR4 is the clear choice due to its ability to resist fire.
If mechanical strength, chemical resistance, and dielectric properties are more important, and flame retardance is not required, G-10 may be the better option despite the higher cost.
Conclusion
Both G-10 and FR4 have their unique advantages, making them suitable for different applications. While FR4 is more common in PCB manufacturing due to its flame retardant properties and lower cost, G-10 is often chosen for applications where superior mechanical strength and dielectric properties are necessary. Understanding these differences will help you make an informed decision, ensuring that your materials meet the specific demands of your project.
By choosing the right material based on the outlined factors, you can optimize both performance and safety, ensuring the longevity and reliability of your products.
tags:oil-immersed transformertransformer procurementsmall factories transformerdry-type transformertransformer cost
- more+releated article
- 2025-08-29Transformer Procurement for Small and Medium-S
- 2025-08-29Applications of NMN Insulation Paper in Low-Vo
- 2025-08-28Transformer Capacity Calculation Step-by-Step:
- 2025-08-28The Role of NMN and AMA Insulation Paper in El
- 2025-08-27High-Efficiency, All-Copper Dry-Type Three-Pha
- 2025-08-27The Impact of NHN and AHA Insulation Paper on
- 2025-08-26High-Efficiency, Energy-Saving Substation Tran
- 2025-08-26Comparing NHN and AHA Insulation Paper in Moto
- 2025-08-26Box-Type Transformers: Dry-Type or Oil-Immerse
- 2025-08-25NHN vs. AHA Insulation: Key Differences and Wh