laminated tube manufacturing process
2024-01-11 17:12 | By: ZTELEC-www.ztelecgroup.com | 147click
The manufacturing process of laminated tubes involves several steps to produce a versatile and durable packaging solution. Laminated tubes are commonly used for packaging various products such as creams, gels, ointments, and other semi-solid substances. Here is a general overview of the laminated tube manufacturing process:
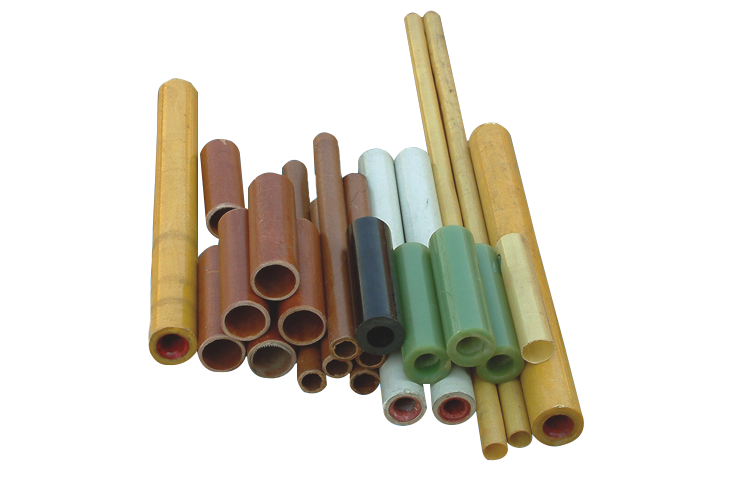
Material Selection:
Choose suitable materials for the tube construction. Laminated tubes typically consist of multiple layers, including a barrier layer, adhesive layer, and outer layer. Common materials include aluminum, plastic, and various barrier films.
Printing and Design:
Design the artwork and graphics for the tube. Printing is often done using advanced printing technologies, including flexographic or rotogravure printing, to achieve high-quality and detailed designs.
Tube Body Formation:
Create the basic tube structure by laminating the selected materials together. This process involves combining the layers through heat and pressure to form a seamless tube.
Extrusion of Plastic Layers:
Extrude plastic layers that will be used in the tube structure. These layers may include the inner and outer layers of the tube.
Aluminum Layer Application:
Apply a thin layer of aluminum to the plastic layers. The aluminum layer serves as a barrier to protect the contents of the tube from external factors such as light, air, and moisture.
Adhesive Application:
Apply an adhesive layer to bond the different layers together. The adhesive ensures that the tube maintains its structural integrity and provides a secure barrier.
Curing and Lamination:
Cure the adhesive through a controlled heating and cooling process. This step bonds all the layers together, creating a strong and cohesive laminated structure.
Tube Formation:
Cut and shape the laminated material into individual tube bodies. This process can be done using cutting and molding machines.
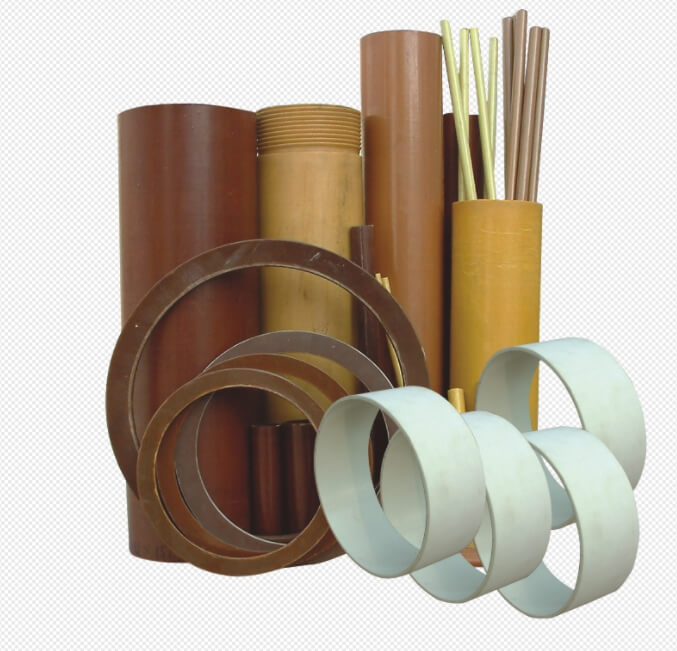
Shoulder Formation:
Form the shoulder of the tube, which is the area near the tube cap. This is often done by folding and sealing the laminated material to create a reinforced shoulder.
Printing of Batch Information:
Print batch and product information on the tubes. This information includes manufacturing date, batch number, product details, and other relevant information.
Cap Attachment:
Attach the tube cap or closure. The cap is usually designed to provide a secure seal and prevent leakage of the tube contents.
Quality Control and Inspection:
Conduct quality control checks and inspections throughout the manufacturing process to ensure that each tube meets the required standards and specifications.
Packing and Distribution:
Pack the finished tubes into appropriate packaging for distribution. This may involve bundling, boxing, or other packaging methods.
tags:150KVA transformertransformer for medical equipmentthree-phase isolation transformerdry-type transformerenergy efficient transformer
- more+releated article
- 2025-06-16High-Performance GPO-3 Sheets for Electrical I
- 2025-06-16Top 5 Advantages of 150KVA Three-Phase Isolati
- 2025-06-13Treatment Methods for Cracks in the Steel Core
- 2025-06-13[Ztelecgroup Mid-Year Promotion] Special Offer
- 2025-06-12Advantages and Disadvantages of GPO-3 Sheets i
- 2025-06-12Top Noise Sources in Isolation Transformers an
- 2025-06-11GPO-3 Laminate Sheet: Benefits, Limitations &a
- 2025-06-11The Future of Power Distribution: Why Dry-Type
- 2025-06-10hy Are 35kV Transformers More Compact Than 10k
- 2025-06-09Innovations and Breakthroughs in Dry-Type Tran