The difference between fr4 and g10
2023-12-14 18:03 | By: ZTELEC-www.ztelecgroup.com | 60click
FR4 and G10 are both types of glass epoxy laminates used in the production of printed circuit boards (PCBs) and various other applications. While they share similarities, they also have differences in terms of composition, properties, and applications.
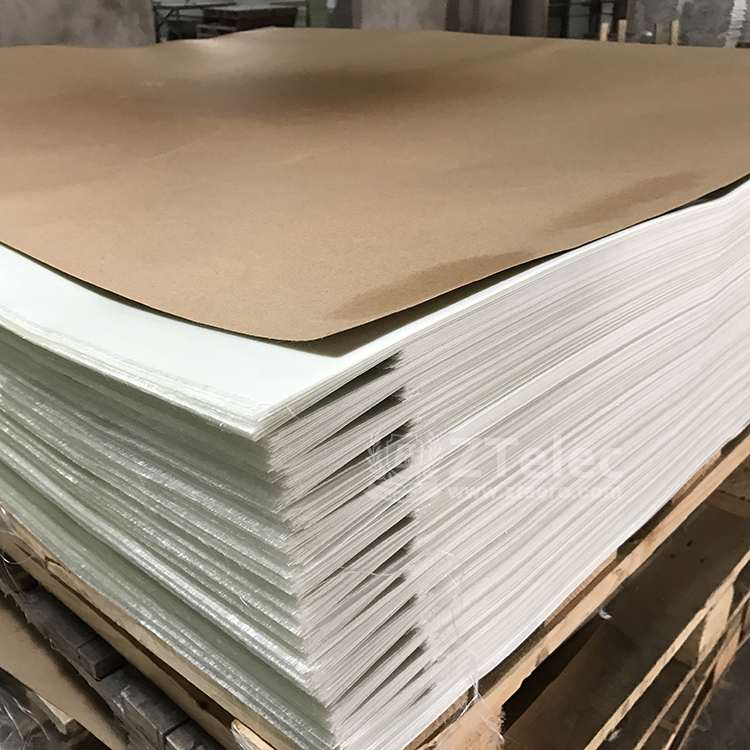
1. Composition:
FR4:
FR4 is a flame-retardant composite material that consists of a woven fiberglass cloth impregnated with an epoxy resin.
The "FR" in FR4 stands for "flame retardant," indicating that it has fire-resistant properties.
G10:
G10 is also a glass epoxy laminate, but it is often composed of woven fiberglass cloth impregnated with a different type of epoxy resin known for its high-pressure laminate properties.
The "G" in G10 stands for "glass."
2. Flame Resistance:
FR4:
FR4 is specifically designed to be flame-retardant, making it a preferred choice for applications where fire safety is a concern.
G10:
G10 may not have the same level of flame resistance as FR4, and its selection for applications involving fire safety may depend on the specific resin used.
3. Mechanical Properties:
FR4:
FR4 is known for its good mechanical strength, dimensional stability, and electrical insulation properties.
It is a widely used material for PCBs due to its combination of strength and electrical performance.
G10:
G10 is recognized for its high mechanical strength and rigidity, making it suitable for applications where structural integrity is crucial.
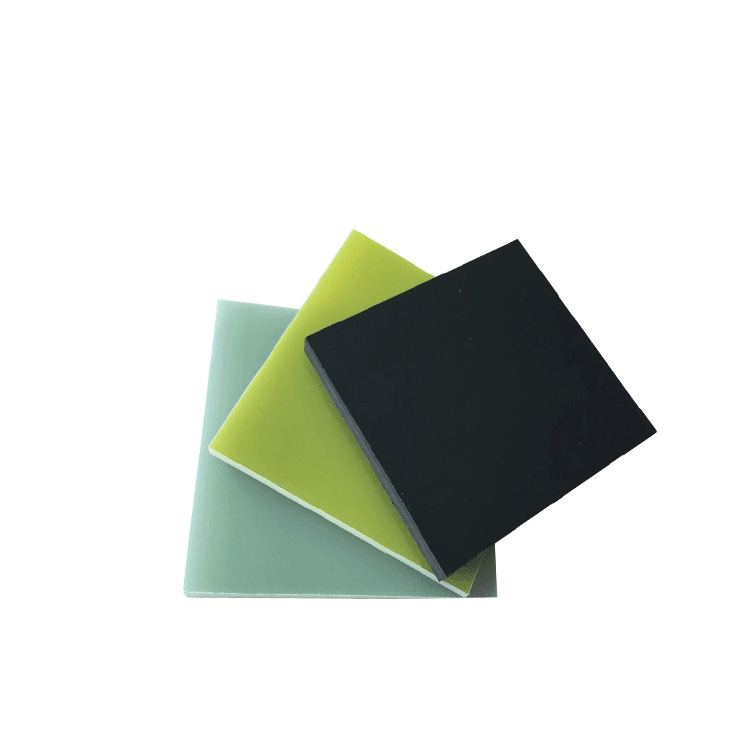
4. Electrical Properties:
FR4:
FR4 offers good electrical insulation properties, making it suitable for PCBs and electrical applications.
It is known for its relatively low dielectric constant and dissipation factor.
G10:
G10 also provides good electrical insulation properties and is often used in applications where both electrical and mechanical performance are important.
5. Applications:
FR4:
FR4 is commonly used in the electronics industry for manufacturing PCBs, insulating materials, and other components where flame resistance and electrical insulation are essential.
G10:
G10 is utilized in various applications, including structural components, knife handles, gears, and other parts where high mechanical strength and dimensional stability are required.
In summary, while FR4 and G10 are both glass epoxy laminates, FR4 is specifically designed with flame retardancy in mind, making it a preferred choice for applications with fire safety considerations. G10, on the other hand, is known for its high mechanical strength and is often used in structural applications. The selection between FR4 and G10 depends on the specific requirements of the intended application.
tags:oil-immersed transformertransformer procurementsmall factories transformerdry-type transformertransformer cost
- more+releated article
- 2025-08-29Transformer Procurement for Small and Medium-S
- 2025-08-29Applications of NMN Insulation Paper in Low-Vo
- 2025-08-28Transformer Capacity Calculation Step-by-Step:
- 2025-08-28The Role of NMN and AMA Insulation Paper in El
- 2025-08-27High-Efficiency, All-Copper Dry-Type Three-Pha
- 2025-08-27The Impact of NHN and AHA Insulation Paper on
- 2025-08-26High-Efficiency, Energy-Saving Substation Tran
- 2025-08-26Comparing NHN and AHA Insulation Paper in Moto
- 2025-08-26Box-Type Transformers: Dry-Type or Oil-Immerse
- 2025-08-25NHN vs. AHA Insulation: Key Differences and Wh